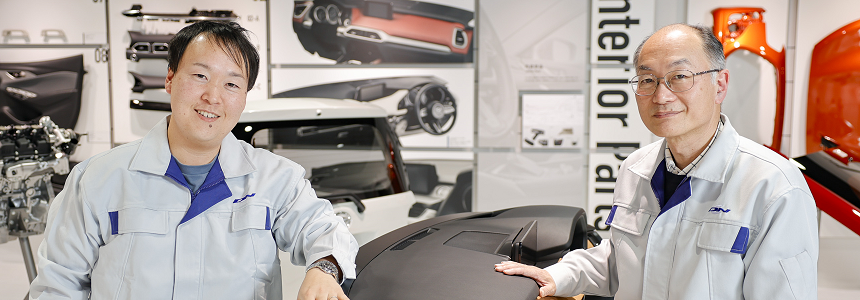
経年劣化の課題を克服したインストルメントパネルの『PVC表皮』
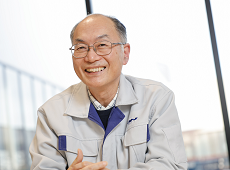
インストルメントパネルの表皮は、樹脂の柔らかさを保つための可塑剤を多く含んでいます。そのため、可塑剤が溶け出すことで表面がベタつくという課題がありました。また、夏場は強い直射日光にさらされ高温になり、長期間この環境にさらされるとインストルメントパネルの表皮内部の可塑剤が奪われて縮んでしまい、表皮がめくれたりひび割れがおきたりするといった劣化の課題もありました。
PVC(ポリ塩化ビニル)の性質上仕方のないこととはいえ、この課題を解決できないかと何年もの間研究と改良を重ねてきた結果、PVC材料としては革新的な、年月を経ても変化しない触感の良い表皮成形技術の開発に成功しました。
PVCに加える可塑剤・安定剤の種類や配合する分量を幾通りにも変えて検証と評価を繰り返し行い、最終的には元素の結合レベルまで原因となる影響因子を突き詰めて挑戦し続け、ようやく目標とする結果に到達することができました。
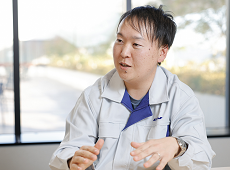
今回の開発では、材料メーカーである龍田化学株式会社と協働し、パウダースラッシュ成形に最適な材料を使用することで、理想的な表皮成形がみえてきたものの、量産にこぎつけるまでには多くのスペックを満足させなければなりません。
最も苦労したのは、エアバックの開き方のレギュレーションをクリアすることでした。表皮を開発する中では、表皮だけを改良すればよいというものではなく、インストルメントパネルに必要となる安全性などのスペックまで検証しクリアさせていかなければならず、様々な状況下を想定した実験を何度も行いました。ようやく全てをクリアできた時は本当に嬉しかったです。今回開発したPVC表皮は、優れた製品であることが認められ、この度「“超”モノづくり部品大賞」で「モビリティー関連部品賞」を受賞することができ、量産化に尽力いただいた関係部署の方々に感謝するとともに、これまでの努力が報われた気持ちです。
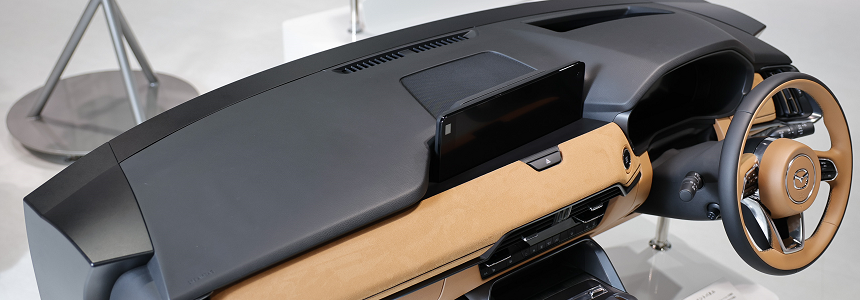
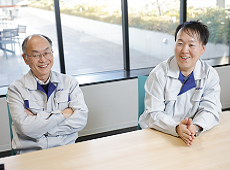
ユーザーが目にして手で触れる表皮にとって見た目や触感はもちろん大切ですが、インストルメントパネル全体で考えると最優先はやはり安全性です。思ったような結果はなかなか出ないですし、一つをクリアすれば別の不具合が生じる相反もよくあるので、表皮の材料としてPVCを諦めようと思ったことも正直ありましたが、安心して乗っていただけるモビリティーでなければならないことを常に意識し、日々実験に取り組んできました。
今回の開発で表皮開発は終わりではありません。今後は、布調のような、これまでの表皮とは異なる触感の開発に挑戦してみたいと考えています。それと同時に、技術やノウハウが途切れることのないよう次世代への伝承と育成を行い、快適性や機能向上などの付加価値を高める技術を追求していきたいです。