当社は、お客様の要求性能を満足させる樹脂材料の自社開発、自動車・住宅設備部品に関わるあらゆる樹脂部品の研究に対して創造的なチャレンジを継続し、多くの可能性を秘めた樹脂の高機能化を進め急速な電動化・環境変化など未来に向けた、より付加価値の高い研究開発・技術開発に取り組んでいます。
また、製品やシステムに要求されている機能・性能を満足させるだけでなく、お客様へ提供する価値を最大限に引き出す最適な製品設計を行います。製品設計からCAE検証・実機評価を一貫して行うことで、より質の高い製品開発を実現し、軽くて形状自由度が高いプラスチックの特性をさらに高め、機能性・安全性・強度・耐久性・環境配慮など、付加価値の高い製品の提供を目指し、開発に取り組んでいます。
さらに、持続可能な社会へ貢献するため資源のリサイクルや自然エネルギー、再生可能エネルギーの利用、エネルギー損失の少ない設備の開発と導入、自働化の推進により新たな技術開発へ人財を投入し社会環境の変化に対応し、地域、社会とともに成長し続けるものづくりの技術集団として常に前進し続けます。
これらの研究・開発・技術が三位一体となりものづくりを行うことで、新しい価値を積極的なチャレンジで創造し、プラスチックの新たな可能性を拓く提案型企業を目指します。
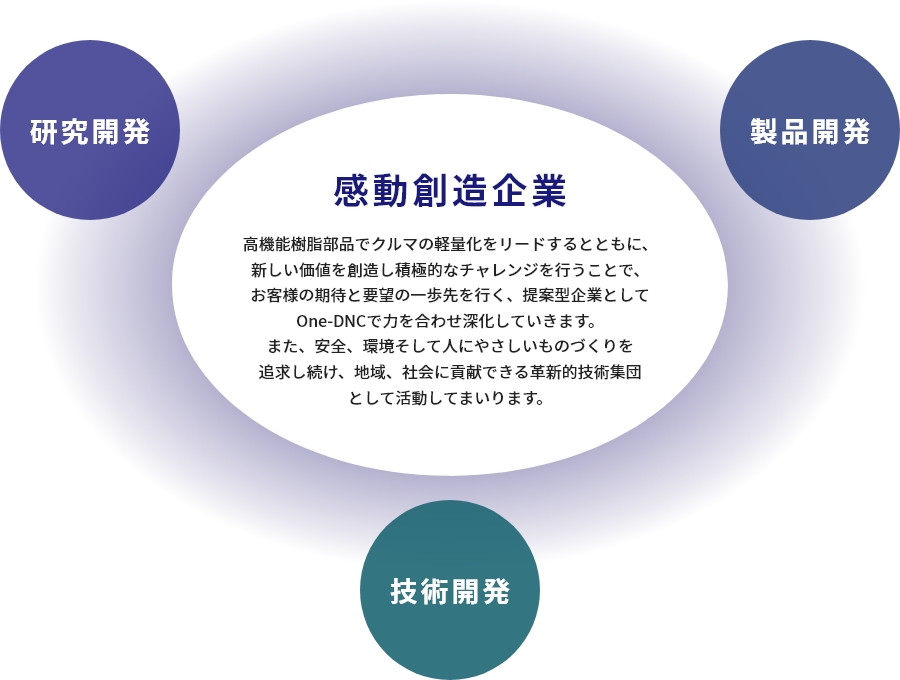
(クリックして拡大)
研究開発
樹脂の新しい可能性を追い求めて
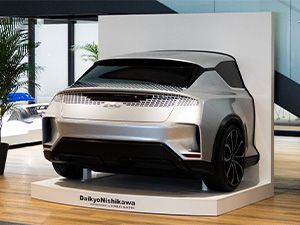
まだ市場に投入されていない製品や技術を開拓するため、ニーズ・シーズの動向調査から研究開発、製品化まで多岐にわたる業務に取り組んでいます。
また産学官連携にも注力し、大学や研究機関との共同研究を進めています。研究員一人ひとりが新しい風を取り込む重要な役割を担い、樹脂の可能性にチャレンジし続けながら社会貢献に努めています。
研究開発
製品開発
創造的・革新的な製品開発で感動を創造する
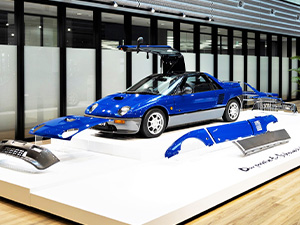
CASEやMaaS、サステナビリティ等、変化し続ける自動車業界において、サプライヤーである私たちはお客様のニーズへ貢献していく使命があります。開発から生産まで一貫して自動車メーカーへ直接製品をお届けする強みを生かし、当社独自の革新的な製品開発で顧客ニーズと市場動向を先取りし、感動を創造していきます。
製品開発
技術開発
オンリーワンを目指した技術開発
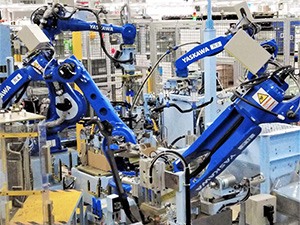
ニーズを先取りした製品で必要とされる新たな技術の実現に向け取り組んでいます。生産数の変動にもフレキシブルに対応できる自働化推進と、設備の省エネ、再エネや自然エネルギーの利用により環境にやさしいものづくり開発を目指し、持続可能な社会に積極的に取り組んでいきます。
技術開発