Production engineering is to build a production system and environment for high quality and efficient mass production of developed products.
Our production preparation, which is based on a production site maintenance plan and product designs, spans from the design of the plant building to large manufacturing facilities such as painting and assembly equipment as well as miscellaneous equipment such as flat trolleys and conveyance systems.
Currently, having put digital tools to full use, we strive to meet customers’ quality requirements at a higher level and to make our Monozukuri friendly to people and the environment.
- Research/
Planning
- R&D
- Product design
- CAE
- Testing and evaluation
- Production engineering
Molding Technology
The molding technology is used in the first process of our Monozukuri and is essential to our products. There are two types of plastic materials: thermoplastic and thermosetting. We select the most suitable plastic material and molding method and analyze mold structures according to product characteristics, functions, and operating environment. The result is fast-cycle, high-quality production of all products.
Thermoplastic are used in many products such as interior, exterior, and functional parts.
Thermosetting plastics are often used in electric vehicles, replacing ferrous and non-ferrous metals.
Battery cover
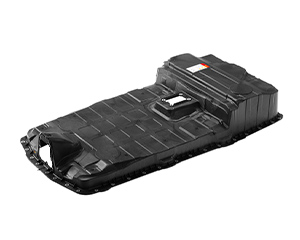
Battery cover products made of plastic, contributing to weight reduction, reduce motive energy consumption and help reduce CO2 emissions.
Plastic cooling pipes
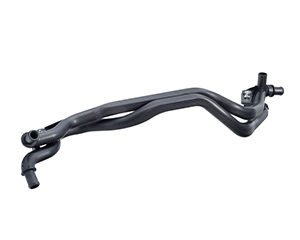
Hollow-molded plastic pipes with a high degree of freedom in shape and applicability to complex paths and shapes are produced by gas-assisted injection molding. Gas has the property of flowing in the direction which, for it, is easy to flow. With this property in mind, we develop product designs and mold structures and control molding and gas injection conditions to ensure stable quality during manufacturing. Use of pipes molded by this method to cool a battery enables weight reduction and contributes to reduced CO2 emissions.
Waste from the manufacturing process has been reduced to zero (100% recycling rate).
Engine cover
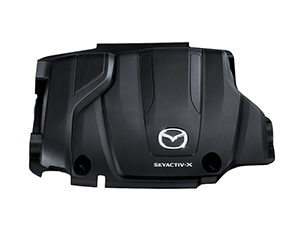
We use foam molding to satisfactorily improve the appearance as seen when you open the hood and to reduce the weight.
To avoid appearance defects specific to foam molding, we use several measures including, in addition to material development, the following: control of molding conditions, control of sensors installed in the mold (pressure and temperature), and control of mold behavior by monitoring to the order of the dimensional tolerance during manufacturing.
CAE analysis
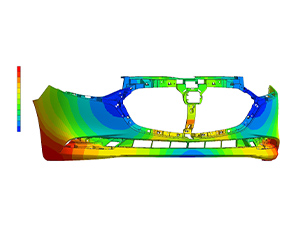
Reproduction analyses are performed to minimize the difference between analysis results for plastic flow and warp deformation and actual machine data. The analysis is meant to obtain results comparable to those obtained using an actual machine, by conducting computer simulation trials. We contribute to reduce the number of trials and to shorter development times.
We will continue to improve the accuracy of analysis on a daily basis with the aim of reaching completion on a single trial. In this way, we strive to conserve the environment.
Decoration Technology
To add various decorations (surface finishes) to molded plastic products, we develop suitable decoration methods and processes, put them into tangible form, and arrange them for mass production.
For instrument panels, we start with the development of materials that provide a comfortable feel appealing to the senses and that do not look degraded in appearance or performance with the passage of time. We then look into engineering methods to bring out the performance, design a process according to the properties of the material, establish good-quality conditions, and build a production line that ensures stable production.
To provide three-dimensional molded surfaces with real stitches, we equipped the sewing machine with an assist, which is a product feed device adaptable to specific design geometries. Thus our stable production process is assured.
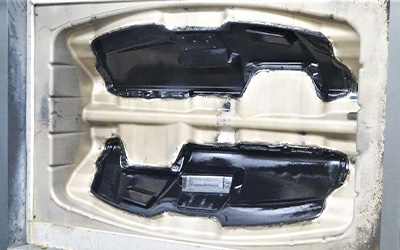
Slush molding
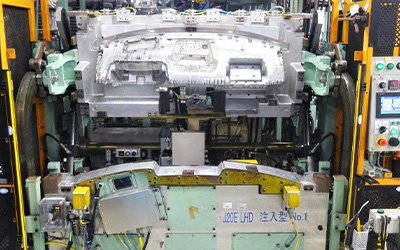
Foam molding
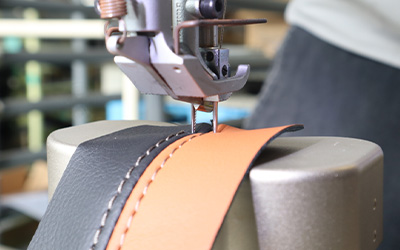
Sewing machine, stitching
Thanks to technological innovation in painting, we have set up an eco-friendly painting line that combines a drying booth and the latest spindle painting capable of painting even on the reverse side of products. We are also making the painting line suitable for water-based paints.
We have developed a defect-free painting process. Painting is done by robots; process simulations are effectively used for the painting trajectory of the target product so as to predict defects.
Leveraging our extensive expertise in painting technology, we constantly take on the challenge of achieving better Monozukuri.
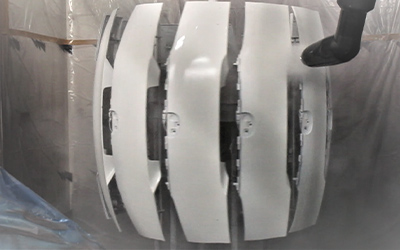
Spindle painting
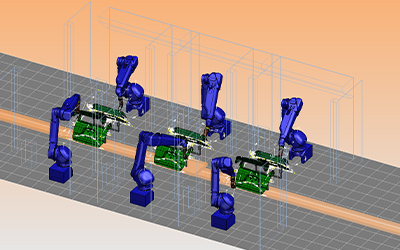
Painting simulation
Assembly Technology
Promoting Generalization of Assembly Process
After the specifications for assembly equipment, jigs, tools, and other devices have been established, we procure and install them during the production preparation period. For successful Monozukuri in the assembly process, it is necessary to build a waste-free, loss-free, high-quality, high-efficiency assembly line that is capable of flexible production.
In addition, due to the trends in social conditions, we are particularly focused on development of autonomous operations. Our efforts are directed toward building a general-purpose autonomous assembly line using robots. We have been making many processes autonomous, including the tailgate assembly line, milling machines, primer coaters, adhesive applicators, material handling equipment, and image-based inspection.
We will continue to focus on automation, ensure stable product quality at a higher level, reduce work-in-progress, and strive to prevent the generation of waste products.
Automatic Tailgate Assembly Line
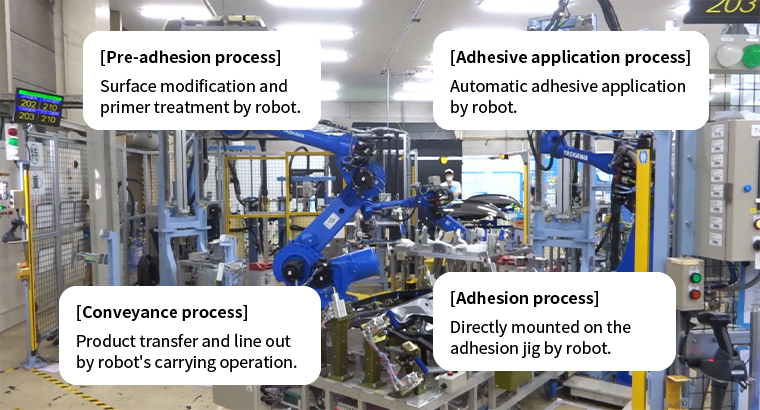
(Click to Enlarge)
Making Assembly Process General Purpose
We have undertaken process simplification by making the process general purpose. By introducing milling machines and other general-purpose machines, we have simplified the plant layout. Moreover, the efficiency of the assembly process has been improved by slimming down and minimizing the operation loss of the assembly process. Furthermore, making it general-purpose enables a model-mixed flexible production line to be set up, reducing the investment in the assembly line and saving space.
Use of Simulations
Our process design incorporates simulations performed in advance, aimed at facilitating operators to work in the most natural posture. Conducting workability verifications and human trajectory analyses, we pursue optimal Monozukuri. Simulations are also used for computer-aided verification of feasibility during the conceptual automation period in the drawing development phase. We are making enhanced efforts to keep up with further digitalization.
Verification of Ease of Operation
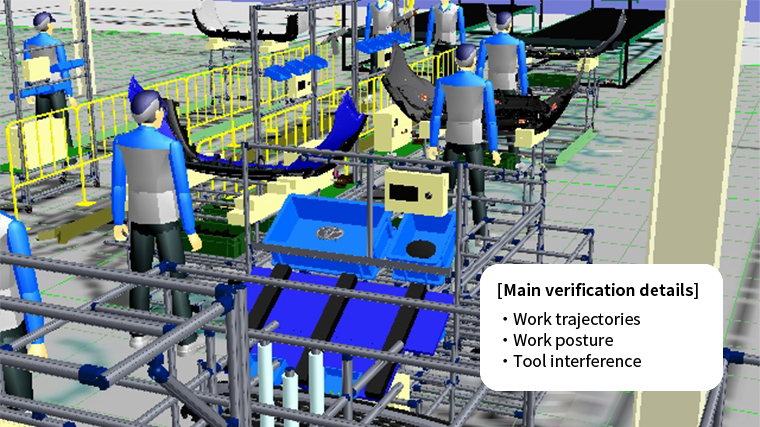
(Click to Enlarge)
Product Evaluation
Aiming to develop even higher technical capabilities and improve product quality, we pursue Monozukuri ensuring that product qualities such as appearance, color, gloss, and dimensional accuracy are better than specifications set out in product drawings. Our goal is to lead the world in the development of vivid, high-precision plastic products through quantitative analysis conducted in addition to visual quality inspection.
In addition, for reliable product evaluation using digital tools to be conducted according to specifications set out in drawings, we provide prompt feedback of the evaluation results to the most upstream part with the aim of improving the processes of development projects. We also aim to stabilize product quality by quantifying and digitizing operations in the sensory domain as much as possible, that is, by making what is invisible visible.
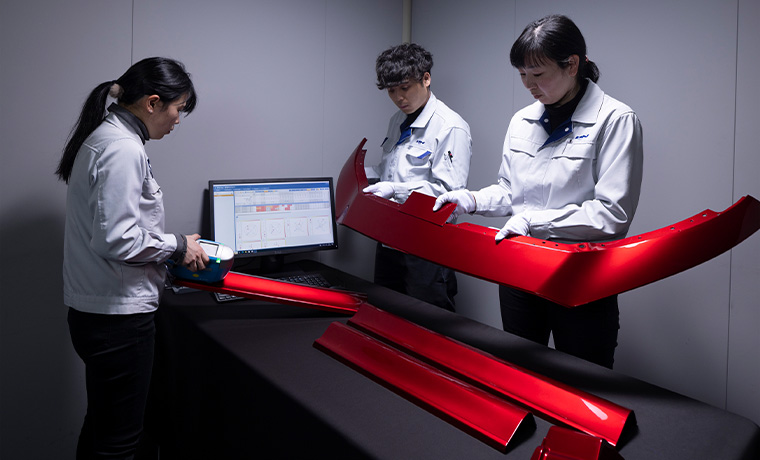
Color evaluation, measurement, and analysis
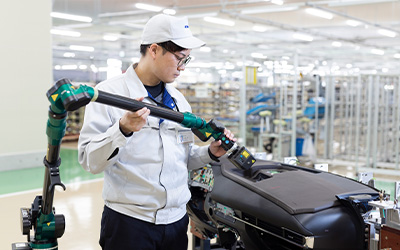
3D measuring instrument
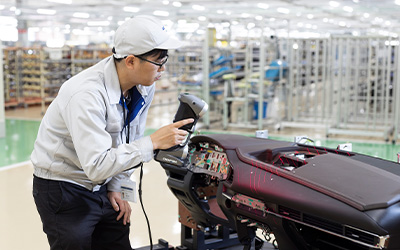
3D handheld scanner
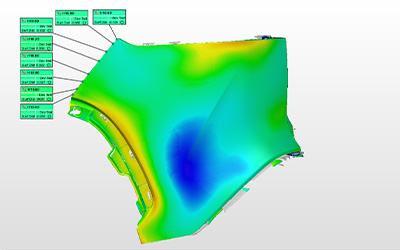
Measurement results
Equipment Engineering
We find out the process and equipment capabilities at all plants and establish specifications for the latest energy-saving, fast-cycle equipment with profitability in mind. In this way, we plan and introduce the ideal capital investment in our manufacturing sites.
Introduction of State-of-the-Art Energy-Saving, Fast-Cycle Equipment and Special Molding Methods and Equipment
Injection Molding Machine
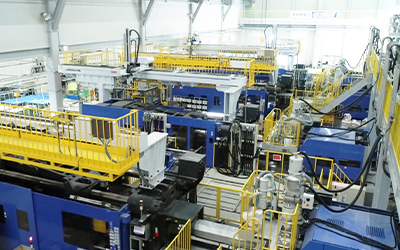
Our efforts toward cutting CO2 emissions and product cost reduction include considering reducing the power consumption of molding equipment and making the equipment fast cycle. For example, by introducing an automatic mold changer, we can change molds safely and quickly, which allows us to respond to the need for high-mix, low-volume production.
In addition, equipment capable of handling special molding methods has been introduced to form a fine-foam layer inside plastic and to produce hollow parts by gas-assisted molding, thus making products considerably more lightweight.
Compression Molding Machine
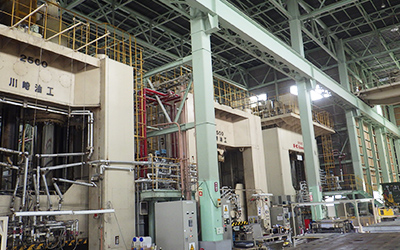
Compression molding machines are used to form products from fiberglass-reinforced Sheet Molding Compound (SMC) materials. The products including bathtubs for homes and large battery covers for electric vehicles are lightweight and rust free.
For the compression molding machine, our CO2 emission reduction efforts include using an accumulator and other devices to reduce motor capacity and making the machine a fast-cycle machine.
Painting Equipment
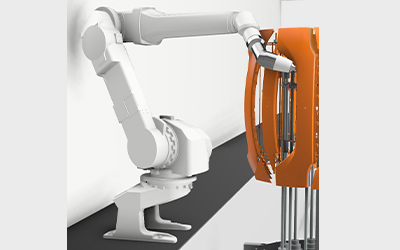
A high-speed color change system has been installed to change the color for each painting jig and improve the production efficiency of painting. We have proactively employed CO2 emission reduction technologies such as the use of water-based paints, optimal air conditioning control for painting booths precisely responding to the outside temperature, and the reuse of most of the heat energy previously released into the atmosphere.
Utilization of Digital Tools
IoT-Based Quality Control
Using the Internet of Things (IoT) to link data from the manufacturing process and inspection equipment and to analyze them, we identify the causes of defects and set optimum-quality conditions.
These data analysis results are used to implement trend control on portions that are demanding in terms of product quality and to prevent defects in advance. In this way, we will maintain a 100% non-defective rate.
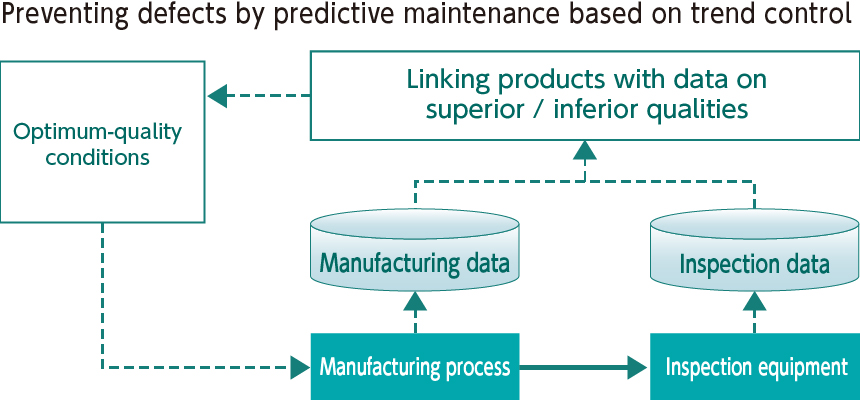
Collect, analyze, and manage data from all automated lines
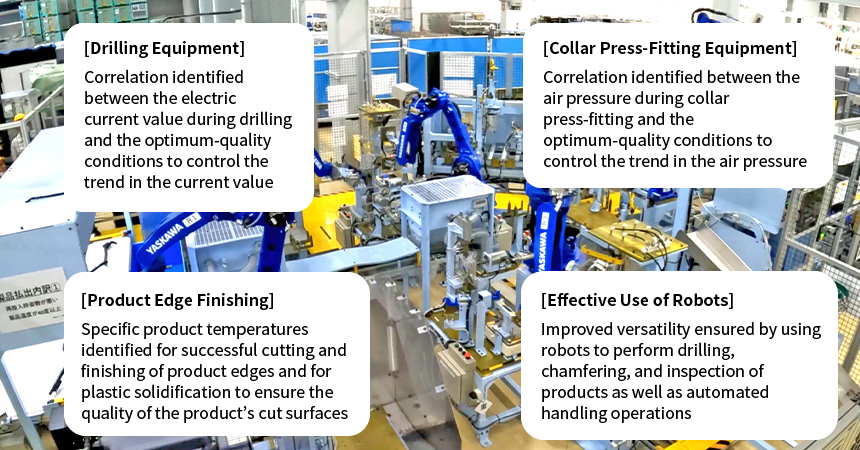
(Click to Enlarge)
Prototype Verification Using a 3D Printer
Prototypes are verified for each process of molding, painting, assembly, and delivery to check the soundness of Monozukuri prior to the completion of production molds or production process, that is, without waiting for the completion of a molded product or a component.
3D data → 3D printer → Formed object
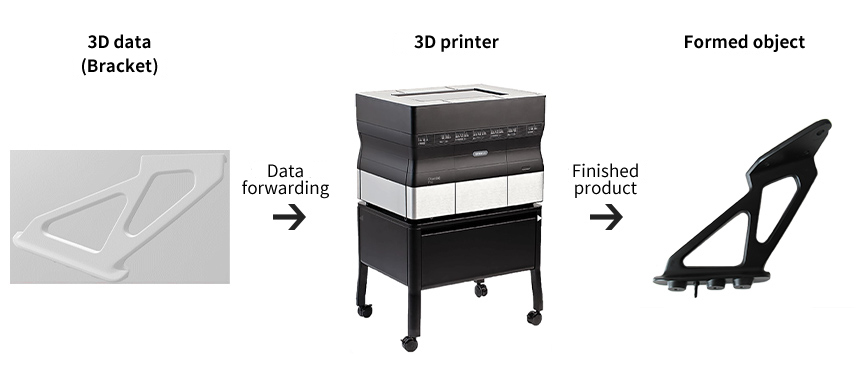