Basic Philosophy
For DaikyoNishikawa, improvement of product quality is an important policy. Also, in fulfilling its responsibilities as an enterprise, DaikyoNishikawa believes quality commitment it is absolutely essential to meet customer requirements. Its action guidelines for that purpose are provided in a clear, visible form as the Quality Policy in the Quality Manual.
Each and every one of us is thoroughly aware of the Quality Policy and proactively works to enhance our organizational strengths. By doing so, we will provide even higher quality products that satisfy our customers.
Quality Policy
We will deliver the “highest satisfaction to customers” by:
- Creating quality through processes with reliable activities,
- Taking into consideration customer needs and expectations in advance to create attractive products, and
- Operating a quality management system effectively for continuous improvements.
Action Guidelines
-
1. What are “reliable activities”?
(i) We make work procedures clear.
(ii) We follow the work procedure.
(iii) We record the results of work.
(iv) We review the procedure and make improvements.
-
2.What are “attractive products”?
We constantly bring about technological innovation and aim for Best in Class (BIC).
-
3. What are“continuous improvements”?
(i) We learn from past failures and do not make the same mistake again.
(ii) We constantly innovate in quality.
Quality Assurance System
To make our quality management system clear, we identify the necessary processes, establish mutual relationships such as inputs and outputs on a process map, and continuously improve them.
The process map summarizes the three processes—main process, management process, and support process—and clarifies the roles and relationships of each organizational unit.
In addition, we incorporate customer requests into the entire process and into the system. We have established a quality management system in which the roles of the design and development processes are clear with support for our global business sites in mind.
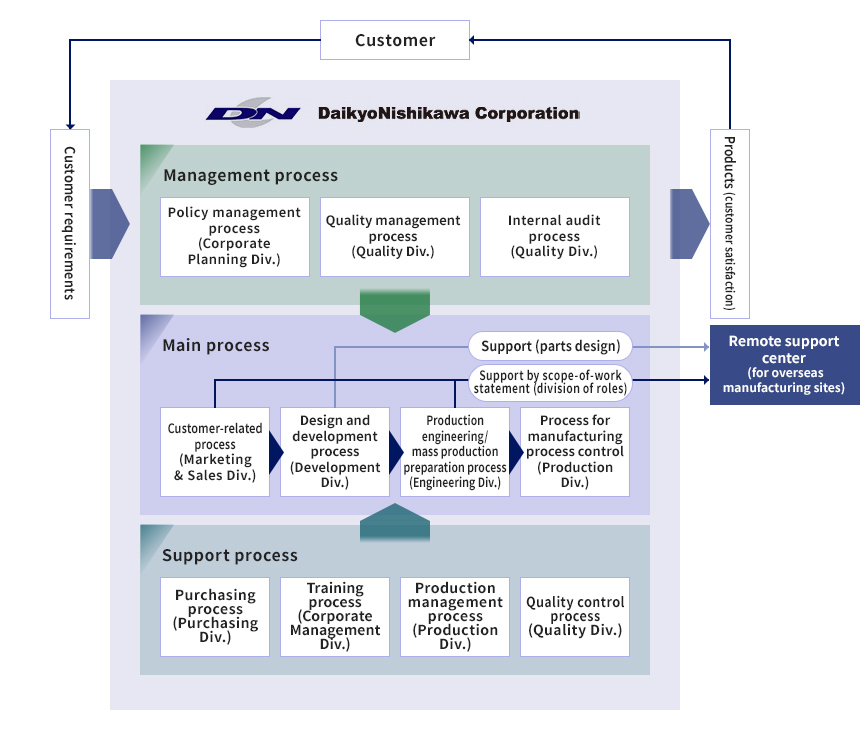
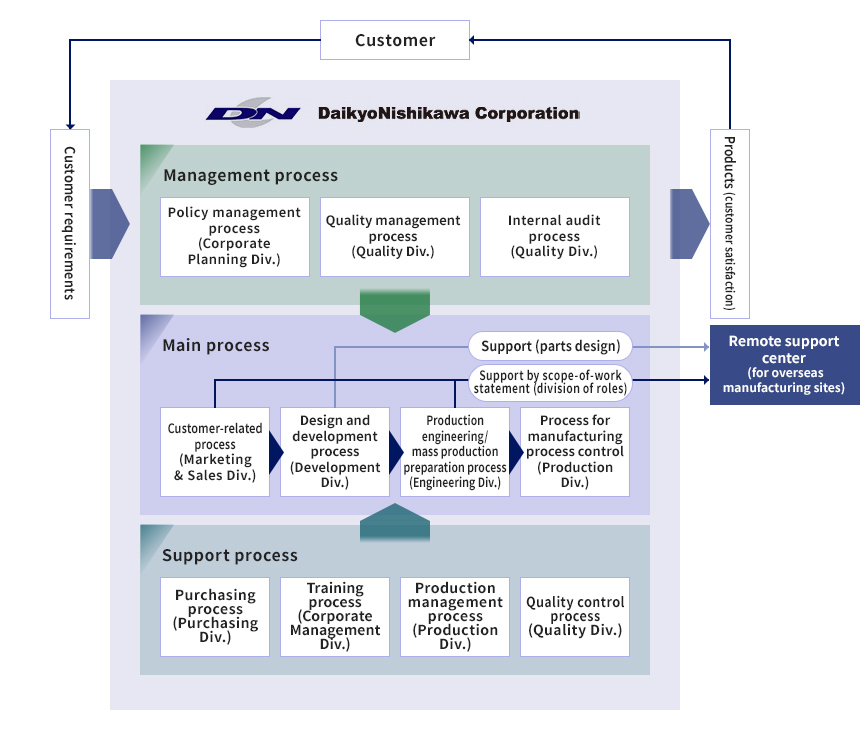
(Click to Enlarge)
Quality Assurance Efforts
We have built our quality management system based on ISO 9001:2015 and IATF 16949:2016. Each division sets quality targets and conducts activities to achieve them. Moreover, an internal quality audit is conducted once a year to clarify issues in each division and make improvements. We work on quality improvements through activities such as analyzing and taking measures to counter potential issues at the product development stage, as well as providing feedback to the source on measures against complaints in the market and against past troubles that occurred at the production site.
Furthermore, we promote quality assurance activities on a full participation basis sharing the awareness all the time that each and every one of us is responsible for quality. At the same time, we are continuously implementing quality training and education programs using internal and external training services.
We focus on activities to align mindset with regard to quality across our group companies, including global business sites. All employees share the same perspective and strive to improve quality.
Certification
ISO9001
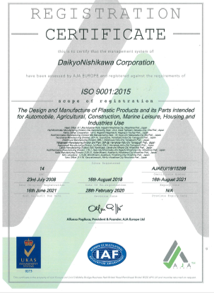
Scope |
The Design and Manufacture of Products and its Parts intended for Automobile, Agricultural, Construction, Marine Leisure, Housing and Industries Use |
Registration date |
23rd July 2008 |
Registration number |
AJAEU19-15298 |
Certification body |
AJA Registrars Ltd |